Fundamental material safety
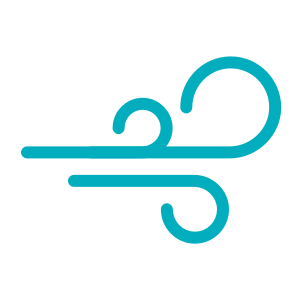
Fundamental material safety
To reduce or eliminate occupant exposure to lead, asbestos, and polychlorinated biphenyls (PCBs) from building materials.
BACKGROUND
Some hazardous materials, such as asbestos, a known human carcinogen, and polychlorinated biphenyls (PCBs), a probable human carcinogen, are currently restricted or banned in many countries, but are often encountered in older buildings. Others, including lead, remain in limited use. Exposure to asbestos fibers through inhalation can occur when building materials degrade over time or are disturbed during renovation or demolition, and is associated with lung cancer and mesothelioma. Exposure to lead can have neurotoxic effects, even at low levels, and in early development is associated with negative effects on memory, IQ, learning and behavior.