Fundamental material safety
- 01 Air quality standards
- 02 Smoking ban
- 03 Ventilation effectiveness
- 04 VOC reduction
- 05 Air filtration
- 06 Microbe and mold control
- 07 Construction pollution management
- 08 Healthy entrance
- 09 Cleaning protocol
- 10 Pesticide management
- 11 Fundamental material safety
- 12 Moisture management
- 13 Air flush
- 14 Air infiltration management
- 15 Increased ventilation
- 16 Humidity control
- 17 Direct source ventilation
- 18 Air quality monitoring and feedback
- 19 Operable windows
- 20 Outdoor air systems
- 21 Displacement ventilation
- 22 Pest control
- 23 Advanced air purification
- 24 Combustion minimization
- 25 Toxic material reduction
- 26 Enhanced material safety
- 27 Antimicrobial activity for surfaces
- 28 Cleanable environment
- 29 Cleaning equipment
- P9 Advanced cleaning
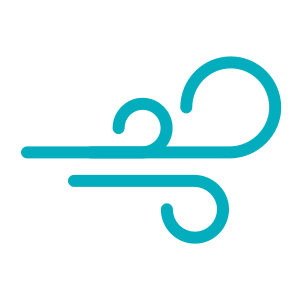
Fundamental material safety
To reduce or eliminate occupant exposure to lead, asbestos, and polychlorinated biphenyls (PCBs) from building materials.
The term “attempt” in this context means the ways in which a project team has tried to procure an appropriate product, which typically involves outreach to manufacturers.
For Parts 2, 3 and 4, projects should draft a short narrative explaining why they are exempt from any or all parts, outlining the rationale for the exemption. This explanation should be submitted as a part of the project documentation.
This feature is applicable only to the WELL project boundary.
For Parts 2, 3 and 4, a project is exempt if the building was constructed after any applicable laws were passed banning or restricting the hazardous material. Part 2 is not applicable if the project is not undergoing demolition, repair, painting or renovation. Part 3 and 4 are not applicable if the project is not undergoing renovation or demolition. However, projects must be sure to adhere to Parts 2, 3 and 4 for any construction occurring after certification to be prepared to comply with this feature at recertification.