Direct source ventilation
17. Direct source ventilation
Indoor sources of pollution can be isolated. Cleaning closets can be a source of harmful chemical vapors, including VOCs linked to carcinogenic, reproductive and developmental issues. Copy rooms can be a source of ozone and particulate matter, which are associated with respiratory and cardiopulmonary diseases. Bathrooms can be a source of mold and mildew that release toxins associated with allergies and asthma.
This feature requires the isolation of indoor pollution sources in separate rooms or exhausted cabinets to minimize their effect on overall indoor air quality. Considerations to minimize risk of exposure include location and adjacency to occupied spaces and restricted access, while direct exhaust helps expel pollutants at the source.
All cleaning and chemical storage units, all areas containing copiers or printers more than 1 m [3 ft] tall and all bathrooms meet the following conditions:
At least 50% (as measured by dollar value) of interior finishes and finish materials, furnishings (including workstations) and built-in furniture have one of the following material descriptions:
The following requirements are met:
The following requirements are met:
The following requirements are met:
Locker rooms, if present, must be ventilated in the following manner:
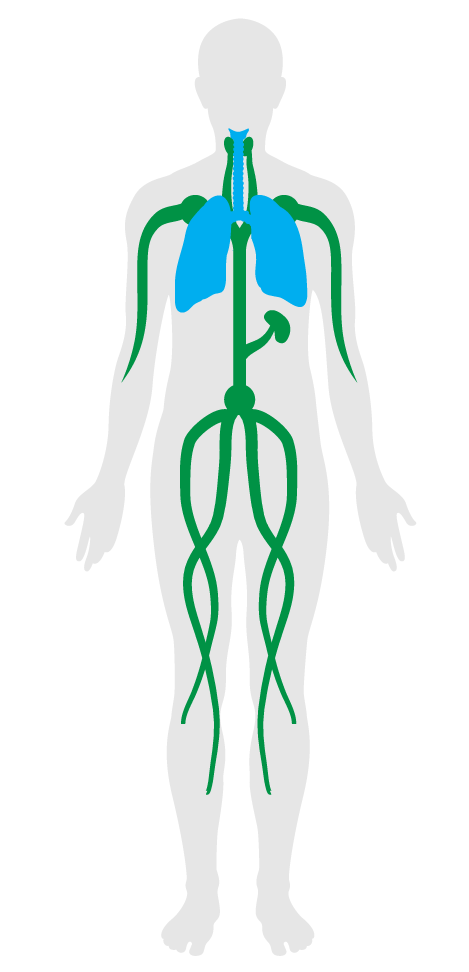
Applicability Matrix
Core & Shell | Tenant Improvement | New Construction | |
---|---|---|---|
Part 1: Pollution Isolation and Exhaust | - | O | O |
Part 1: Material Information | O | O | O |
Part 2: Exhaust Hood Design Guidelines | - | - | - |
Part 3: Makeup air system design | - | - | - |
Part 4: Appliance Guidelines | - | - | - |
Part 5: Locker Rooms | - | - | - |
Commercial Kitchen | Schools | Multifamily Residential | Restaurant | Retail | |
---|---|---|---|---|---|
Part 1: Pollution Isolation and Exhaust | O | O | O | O | O |
Part 1: Material Information | O | O | O | O | O |
Part 2: Exhaust Hood Design Guidelines | O | - | - | - | - |
Part 3: Makeup air system design | O | - | - | - | - |
Part 4: Appliance Guidelines | O | - | - | - | - |
Part 5: Locker Rooms | - | O | - | - | - |
Verification Methods Matrix
Letters of Assurance | Annotated Documents | On-Site Checks | |
---|---|---|---|
PART 1 (Design) Material Information |
Architect | ||
PART 1 (Design) Pollution Isolation and Exhaust |
MEP | Spot Check | |
PART 2 () Exhaust Hood Design Guidelines |
MEP | ||
PART 3 () Makeup air system design |
MEP | ||
PART 4 (Design) Appliance Guidelines |
Architect | ||
PART 5 (Design) Locker Rooms |
MEP |
17.1.b |
USGBC's LEED v4 EQ Credit: Enhanced Indoor Air Quality Strategies requires no recirculation of air in spaces where hazardous gases or chemicals may be present or used (e.g., garages, housekeeping and laundry areas, and copying and printing rooms). |
17.2.a |
The California Energy Commission's Design Guide suggests installing side and/or back panels on canopy hoods. |
17.3.a |
The California Energy Commission P500-03-034F provides design suggestions for commercial kitchen ventilation systems, including minimizing the makeup air velocity near the hood, noting that the velocity should be less than 75 fpm. |
17.5.a |
The guide notes that air from locker rooms should not be re-circulated. |
17.5.b |
The guide notes that the HVAC system should exchange air once about every 45 minutes, which is equivalent to 1.33 air changes per hour. |
17.2.b |
ANSI/ASHRAE 154-2011 states that type II hood overhangs "shall comply with Table 3 on all open sides, measured in the horizontal plane from the inside edge of the hood to the edge of the top horizontal surface of the appliance." |
17.2.c |
ANSI/ASHRAE 154-2011 specifies that "the vertical distance between the front lower lip of the hood and appliance cooking surface shall not exceed 4 ft". |
17.4.a |
The ANSI/ASHRAE Standard 154-2011 provides appliance duty levels for light, medium, heavy, and extra-heavy appliance duty levels based on required exhaust airflow rates for cooking processes. |
17.4.c |
ANSI/ASHRAE Standard 154-2011 defines cooking processes that require exhaust airflow rates of 300 cfm/ft or greater as either "heavy" or "extra-heavy" cooking. |
17.3.c |
The 2013 Supplement to Standard 189.1-2011 notes that "at least 50% of all replacement air must be transfer air that would otherwise be exhausted." |
17.4.b |
The supplemental research document to ASHRAE 1202-RP notes that "adding a rear appliance seal reduced the exhaust rate to 2700 cfm." |
17.3.b |
ANSI/ASHRAE/IES Standard 90.1-2010 section 6.5.7.1.1 states that "replacement air introduced directly into the hood cavity of kitchen exhaust hoods shall not exceed 10% of the hood exhaust airflow rate." |